Media facility provides unparalleled services to UArizona investigators
The BIO5 Media Facility has supplied UArizona researchers with top-of-the-line reagents, dishwashing and project support for nearly 15 years.
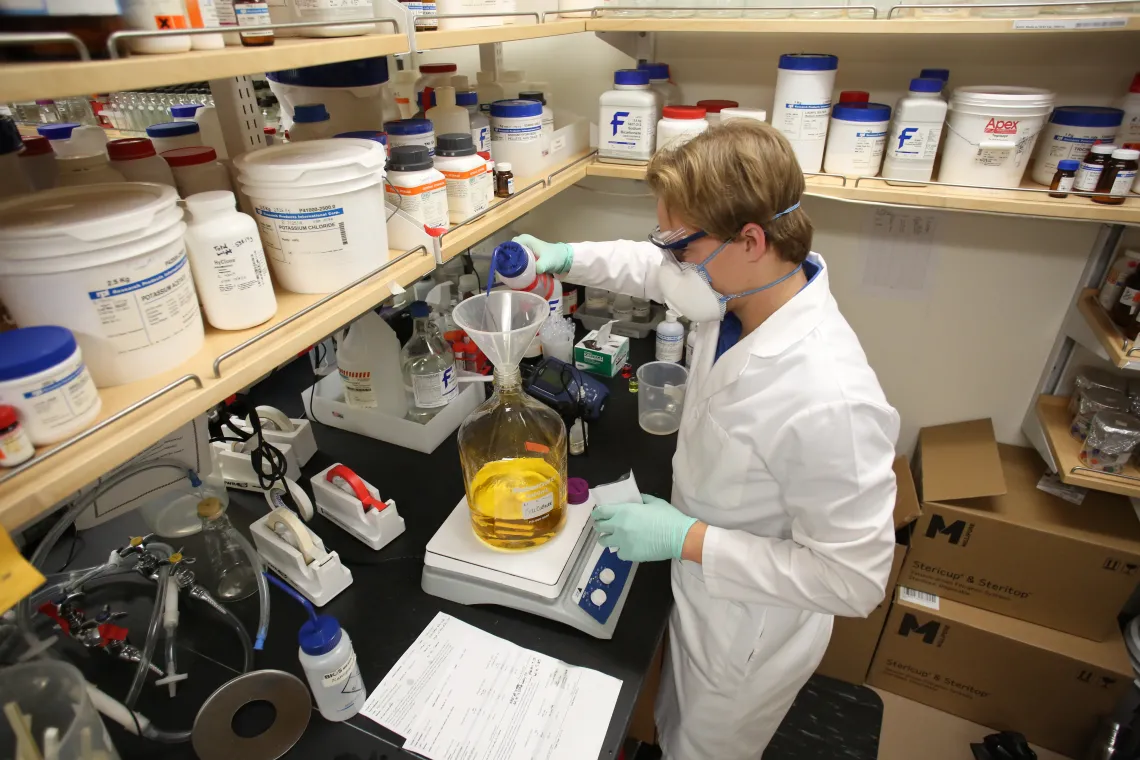
Hidden in the basement of the Thomas W. Keating Bioresearch Building at the University of Arizona, the BIO5 Media Facility provides high-quality research materials, dishwashing, and intellectual support to university investigators at significant cost savings.
This service allows researchers to improve efficiency, strengthen their ability to receive and fulfill grant applications, and more swiftly move their innovations forward to impact the biomedical and biological sciences. This BIO5 core service has grown to serve more than 150 UArizona laboratories and academic units since its establishment in 2007.
High quality products at a low price
While superior products often come at a great expense, the Media Facility prides itself on providing high quality at an exemplary value. The facility’s cost savings are a result of the ability to order supplies in bulk quantities. In addition to the wholesale discount, special pricing from vendors also enables the facility to offer researchers lower costs for the same products they normally buy directly from each retailer.
“Because of our ability to order in bulk and receive special discounts from popular vendors, the individual labs save money, allowing them to use their grants on other necessary aspects that support their research,” administrative manager Tamara Sprung said.
In addition to supplying researchers with pre-made products from big-name vendors, the Media Facility specializes in homemade formulations. The facility prepares large batches of common solutions and growth media needed to support bacteria, plant or animal cell growth. Many researchers purchase their supplies from the Media Facility because the process of making their own supplies can be labor intensive and expensive, taking precious time and resources away from their research.
Designated as a Good Laboratory Practices (GLP) facility, the Media Facility strives to maintain high standards of excellence and consistency in its in-house products. This special designation ensures product quality, batch-to-batch reproducibility, extensive documentation, and lot traceability, enabling researchers to put their trust into the facility’s products.
Researchers can even order specific, non-commercially available formulations for their unique project needs. Production Manager Jody Nyboer offers her expertise to investigators to help them perfect their experimental design and product formulations. Nyboer draws upon her experience as a research and development chemist to address all aspects from “bench top conceptualization” of researchers’ ideas to production of the facility’s products. She also relies on her expertise as a bench scientist to communicate with the university’s scientists.
“We speak the same language, which makes working together much less complicated,” Nyboer said.
Convenience is key
The facility prides itself on its rapid fulfillment time (48-72 hours) and willingness to deliver products directly to a researcher’s lab, allowing research to continue uninterrupted. The facility also supplies its homemade and commercial products at a Convenience Supply Refrigerator on the main floor of the Keating building, where researchers can access commonly-used research products 24/7.
Alternatively, researchers can purchase products online like they would with any commercial vendor. In 2012, former facility manager Dena Yoder led a successful campaign that allowed the BIO5 Media Facility to become the first UArizona entity to have a punch-out catalog on the Arizona BuyWays website.
As the online platform can be tricky to navigate, current manager Sprung has been known to extend a helping hand to researchers or other lab personnel who are ordering through the BuyWays site for the first, second or tenth time – regardless of whether they are purchasing a Media Facility product.
Sprung plans to create a Standard Operating Procedure (SOP) that will walk through each step of the ordering process. While the SOP will be specific to ordering products from the facility, Sprung aims to make it useful enough for anyone to use when ordering products from other vendors through BuyWays.
The Media Facility also offers dishwashing and sterilization services to university investigators. The facility features several high-powered washers and autoclaves that clean and sterilize scientific glassware, ensuring the equipment is in pristine condition before use in an experiment.
Tackling the pandemic with existing resources
At the onset of the COVID-19 pandemic, Sprung and Nyboer brainstormed the resources they would need to be able to prepare reagents to fight the pandemic. After researching formulations for different testing materials and hand sanitizers, they realized that they already had the majority of necessary supplies on hand – they just needed a greater quantity.
Because of the facility’s existing relationship with various vendors, Sprung purchased bulk quantities of their usual supplies at a discount and received them within a week. Starting in March 2020, the Media Facility produced nearly 10 liters a week of Viral Transport Media – an essential part of the COVID-19 PCR test kit. Nyboer has also led the production of the buffer used in the COVID-19 antibody test. Both of these items were produced through the end of the calendar year.
Nyboer’s training and professional skills enabled her to work with Ryan Sprissler, Staff Scientist and Manager at the University of Arizona Genetics Core, on developing the protocol for making the Viral Transport Medium for COVID-19 test kits. Because she has extensive experience with chemicals and understanding scientific patents, Nyboer was able to advise Sprissler on which substances would be the best options for their needs.
For nearly three months at the pandemic’s onset, Sprung also produced more than 400 liters of hand sanitizer each week for university-wide use.
Student engagement at the Media Facility
The BIO5 Media Facility maintains a commitment to student education by hiring budding UArizona student-scientists. The Media Facility employs anywhere between three and five students at a time, working a combined 60 hours a week to produce food for fly research and deliver products to labs, among other tasks. Through their hands-on work, students gain valuable on-the-job training in a GLP environment.
Much like the BIO5 Media Facility’s student workers, Nyboer worked in a media facility during the entirety of her undergraduate career.
“It was my first science-related job, and now that I’m winding down my career toward retirement, it’ll be my last,” Nyboer said. “What wonderful bookends for the career I’ve always loved.”